What exactly is hardness?
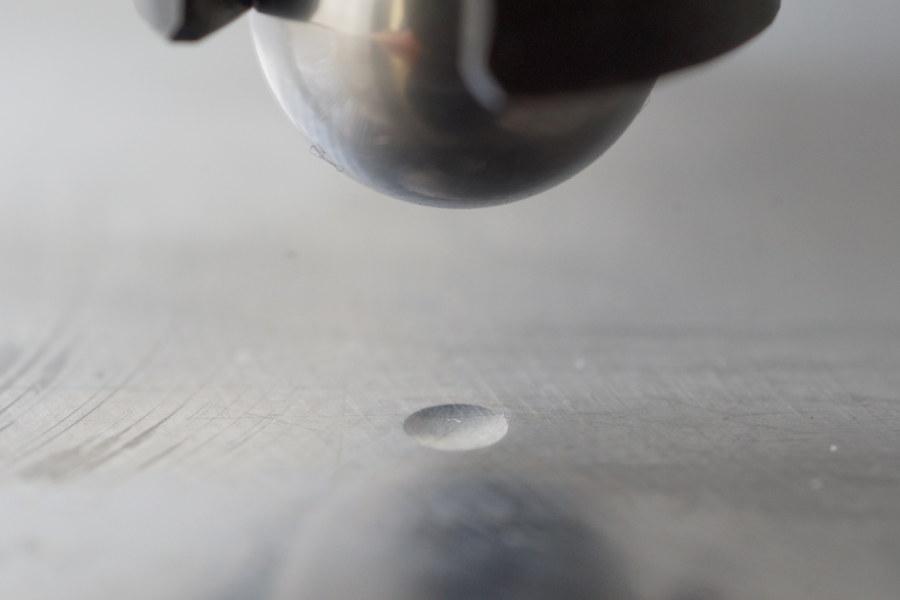
Hardness
Hardness is the resistance of a solid body to be permanently deformed or scratched when it is pushed against a second body. The harder body will always be less scratched or deformed than softer one.
Image | The image above for example shows the indention from a steel ball with Rockwell hardness HRC 64 (actually a roller bearing ball) in a steel plate with hardness HRC 33. The much harder ball remains undeformed. |
There are two basic methods to determine the hardness of a body:
Scratching hardness: | Resistance to scratching by an object of known hardness |
---|---|
Indention hardness: | Resistance to indention by a hard object (e.g. diamond cone) |
Mohs hardness (scratching)
Mohs hardness scale is defined by ten minerals of known hardness on a scale between 1 and 10. The softest (talc) starts with number 1 and the hardest (diamond) is number 10. A harder material always scratches the softer material.
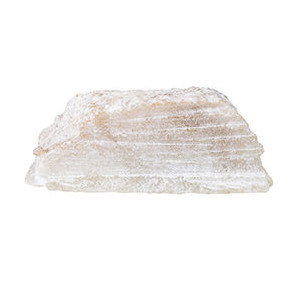
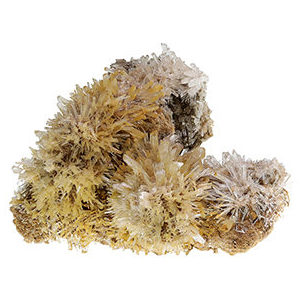

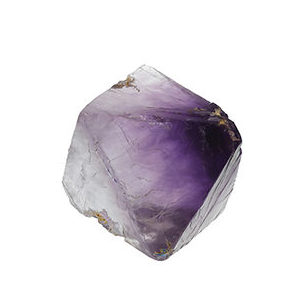
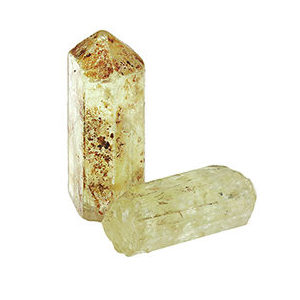
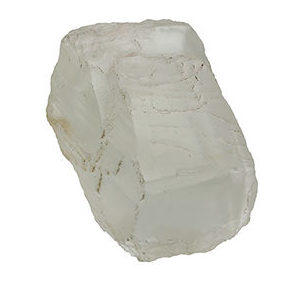
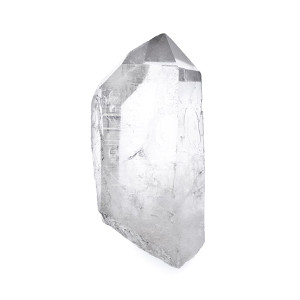
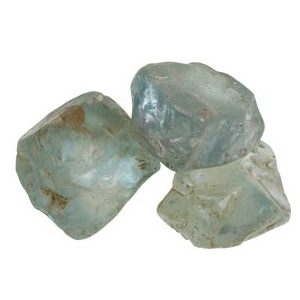
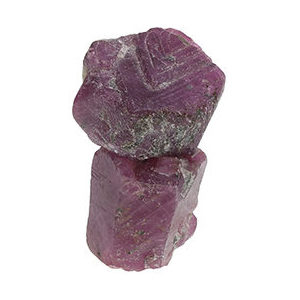
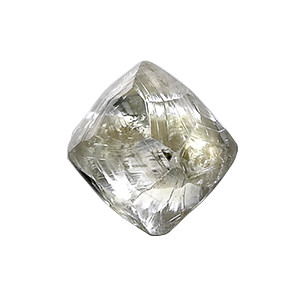
Unfortunately the hardness in-between each of these 10 reference materials is not clearly defined. In addition the whole range of steels, from very soft to very hard, all fall in the range between Mohs 4 and 5. For this reason Mohs hardness scale is not very convenient for engineering applications. Indention hardness is the preferred choice.
Indention hardness
Indention hardness is measuring by how much a hard indentor (e.g. a diamond) is pushed into the testing target under a defined load. Three indention testing methods are commonly used today: Brinell, Vickers and Rockwell. Their key features are summarized in the table below:
Brinell (HB) | Vickers (HV) | Rockwell (HRC) | |
---|---|---|---|
Indentor | 10mm steel ball |
136° diamond pyramid |
120° diamond cone |
Load | 3000 kgf | 0.5-50 kgf | 150 kgf |
What is measured? | size of crater | size of crater | depth of indention |
Speed & simplicity | ★☆☆ | ★☆☆ | ★★★ |
Why three testing methods?
The reason why there are still three hardness testing methods widely used today is, that each of them has its benefits and drawbacks:
- Brinell covers a very wide range of materials and hardnesses but the high testing load (3 ton) and the need for optical measurement of the indent crater size are inconveniences.
- Vickers uses a indentor angle, which has been chosen such, that the result will always be the same independently from which load is applied. Unfortunately it shares the inconvenience of optical measurement with the Brinell method.
- Rockwell has the benefit to be very simple and fast (20~30 seconds for a measurement) and the measurement result is immediately displayed on the testing machine.
Non-destructive – What does that mean?
It is interesting to note, that all three hardness testing methods are non-destructive. That means the object is not damaged apart from small indent craters on the surface. This means the tests can be carried out even on objects which are going to be used in operation. This is in strong contrast to all material strength testing methods, which always result in the destruction of the test sample.
Questions and answers:
Q: How are hardness and strength of a material related?
A: They are very much related, but the answer can not be given in one sentence. So we created a separate blog post - Please have a look HERE.
More related stories:
If you are interest to read more, please check out some of the following blog posts:
Like this post? Please share!
If you like this post and think others might find it useful too, please share it on Facebook, Twitter etc.
Questions? Comments?
If you have questions or comments, please leave us a comment below. We really like to hear back from you! Getting feedback is what keeps us going to write many more articles.
0 Comment
Leave a Comment
Your email address will not be published. Required fields are marked *